Industry 4.0 and Data Science: Mastering Operational Efficiency
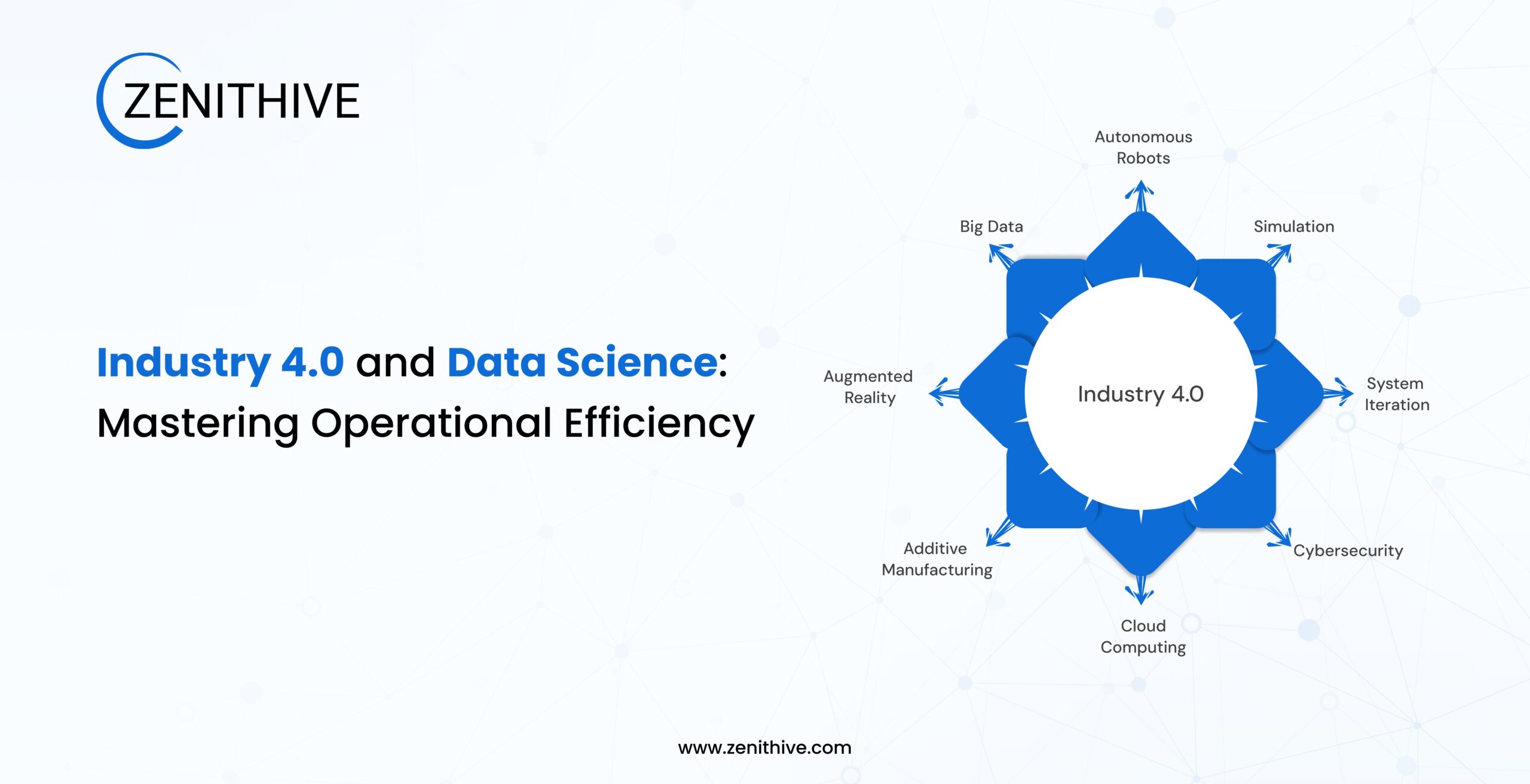
Manufacturers Can’t Afford to Ignore Industry 4.0
The world of manufacturing is changing in ways that might seem unimaginable just a few years ago. Machines that not only talk to each other but also predict when they’ll break down or even suggest how to improve their own performance. This isn’t the stuff of science fiction, it’s Industry 4.0, and it’s already beginning to reshape the entire manufacturing world.
What Exactly is Industry 4.0?
Industry 4.0 is the next evolutionary step in manufacturing. It’s the convergence of cutting-edge technologies like Artificial Intelligence (AI), the Internet of Things (IoT), cloud computing, and automation. It is a revolution in connectivity, where machines don’t just function on their own but work together, share information, and make decisions based on data they gather in real-time.
It’s about transforming the way your factory works, responds to challenges, and grows.
Intrigued? You should be.
What’s Driving the Shift to Industry 4.0?
So, why are manufacturers across the globe rushing to embrace Industry 4.0? The answers might surprise you:
- Unpredictable Markets and Volatile Economies
In today’s world, waiting for “the right time” is no longer an option. Manufacturers need agility, the ability to pivot quickly in response to changing market demands and supply chain disruptions. Industry 4.0 technologies like real-time analytics and AI can equip businesses to make smarter, faster decisions. - Demand for Personalization and Speed
Ever wonder how companies can create custom products for customers, often on demand, and still ship them out in days? The secret lies in Industry 4.0. Automated processes, fueled by data insights, are enabling manufacturers to deliver high-quality products at unprecedented speeds. - The Need for Cost Control
How can a business remain profitable while reducing costs and improving production? Industry 4.0 holds the key. By integrating automation and AI into operations, companies can minimize waste, avoid costly downtime, and boost efficiency in ways traditional methods simply can’t match. - Remote Control of Operations
After the global pandemic, the ability to control operations from a distance became more important than ever. With Industry 4.0, manufacturers can remotely monitor machines, track production, and intervene when necessary, all from the comfort of their own offices or homes. It’s a game-changer.
How is Industry 4.0 Actually Changing Manufacturing?
Now that you know what Industry 4.0 is and why it’s becoming a priority, let’s dig into how it’s making waves in real-world manufacturing. Here’s how it’s already changing the game:
- Smart Machines That Predict Breakdowns
Imagine your machines predicting their own failure before it happens. Thanks to IoT sensors and AI, equipment can send out early warning signs of potential breakdowns, giving you time to fix issues before they become costly problems. No more unexpected downtime! - Supply Chains That Speak to You
Picture this: real-time visibility of your products and materials as they travel through the supply chain, with up-to-the-minute data on their status. This level of insights enables you to adjust quickly when issues arise, keeping operations running smoothly. - Instant Insight into Production
Real-time data from your production lines doesn’t just sit there waiting to be analyzed. Instead, it provides actionable insights that can instantly adjust processes, reduce bottlenecks, and improve efficiency. - Automated Quality Control
No more manual inspections! AI-powered quality control systems can detect defects in real-time, ensuring that products meet the highest standards without the risk of human error. Imagine how much time and money you could save if quality control was faster, smarter, and more accurate.
The Benefits of Industry 4.0 You Can’t Afford to Miss
What if you could increase productivity, reduce waste, and deliver better products to your customers all at the same time? That’s the magic of Industry 4.0. Here’s a look at how this revolution can change everything:
- Smarter Decisions with Real-Time Data
The power of Industry 4.0 lies in its ability to collect and analyze massive amounts of data in real-time. With insights at your fingertips, you can make more informed decisions that drive improvements in production, inventory, and customer satisfaction. The result? A more efficient and responsive business. - Boosted Productivity, Lower Costs
Automation is at the heart of Industry 4.0, freeing up human workers to focus on higher-value tasks. And with fewer errors and less downtime, productivity shoots up while costs drop, a win-win for any business. - Faster Production, Quicker Time-to-Market
Waiting around for products to be made is a thing of the past. Industry 4.0’s agile systems allow manufacturers to adapt to new customer demands and market changes in real-time, accelerating the time it takes to get products to market. - Enhanced Flexibility and Scalability
Want to increase production for a new line of products or scale back when demand drops? With Industry 4.0, you can easily adjust operations without the need for major overhauls or disruptions. - Better Customer Experience
Faster deliveries, higher-quality products, and personalized offerings, it’s all possible with Industry 4.0. The more you can do to meet your customers’ needs, the more loyalty and business you’ll earn in return. - Lower Costs Across the Board
Industry 4.0 doesn’t just help with production, it reduces waste, cuts downtime, and ensures maintenance is done only when necessary. With such efficiencies, your overall costs can decrease significantly, giving your bottom line a much-needed boost. - Easier Compliance with Regulations
Whether it’s safety standards or environmental regulations, Industry 4.0 can help you track, document, and report processes in real-time, making compliance a smoother and less burdensome task.
The Roadblocks on the Path to Industry 4.0
Of course, diving into Industry 4.0 isn’t all smooth sailing. There are a few bumps along the way:
- The Challenge of Integration
Combining new technologies with older systems can be a complex process. Industry 4.0 requires investment not only in new equipment but also in the integration of existing systems, a task that requires time, money, and expertise. - Overwhelming Data Management
With so much data generated, managing and analyzing it all can feel like a daunting task. The right infrastructure and team are critical to ensure this information is being put to good use. - A Workforce That Needs to Evolve
To truly capitalize on Industry 4.0, your team needs the right skills. From machine learning to data analysis, equipping employees with the tools they need to succeed is key to reaping the full benefits of this revolution. - Cybersecurity Concerns
The more connected your systems are, the higher the risk of a cyber attack. It’s essential to implement robust security measures to safeguard your data and keep operations running smoothly. - Upfront Investment
Industry 4.0 comes with a hefty price tag, especially when you factor in technology, training, and implementation. While the long-term benefits are clear, companies must be ready for the initial investment.
How to Begin Your Journey into Industry 4.0
Ready to take the plunge? Here’s how to get started:
- Start Small, Scale Gradually
Begin by testing Industry 4.0 technologies in specific areas where they’ll have the most immediate impact, whether it’s predictive maintenance or real-time inventory tracking. Once you see the benefits, you can scale up to other areas. - Invest in the Right Tech
It’s not just about having the latest gadget. Ensure that your business has the right infrastructure, cloud computing, data storage, and robust cybersecurity solutions, to support Industry 4.0 technologies. - Train Your Team
Ensure your workforce is prepared for the change. Training programs can help your team develop the necessary skills to thrive in an Industry 4.0 environment. - Partner with Experts
Industry 4.0 can be complex, so it’s important to collaborate with technology partners who have the expertise to guide you through the implementation process. - Monitor and Adjust
Industry 4.0 isn’t a one-and-done deal. As you implement new systems, continuously track your progress, gather feedback, and make adjustments to improve your operations further.
The Future Is Now
Industry 4.0 isn’t a distant dream, it’s here, and it’s already reshaping the manufacturing world. The key to thriving in this new era is staying curious, embracing change, and finding the right technologies that can propel your business forward.
The question is, are you ready to take the leap? Connect with Zenithive to take the plunge and let’s reshape your business.