AI-Powered Predictive Maintenance: Reducing Downtime and Costs in Manufacturing
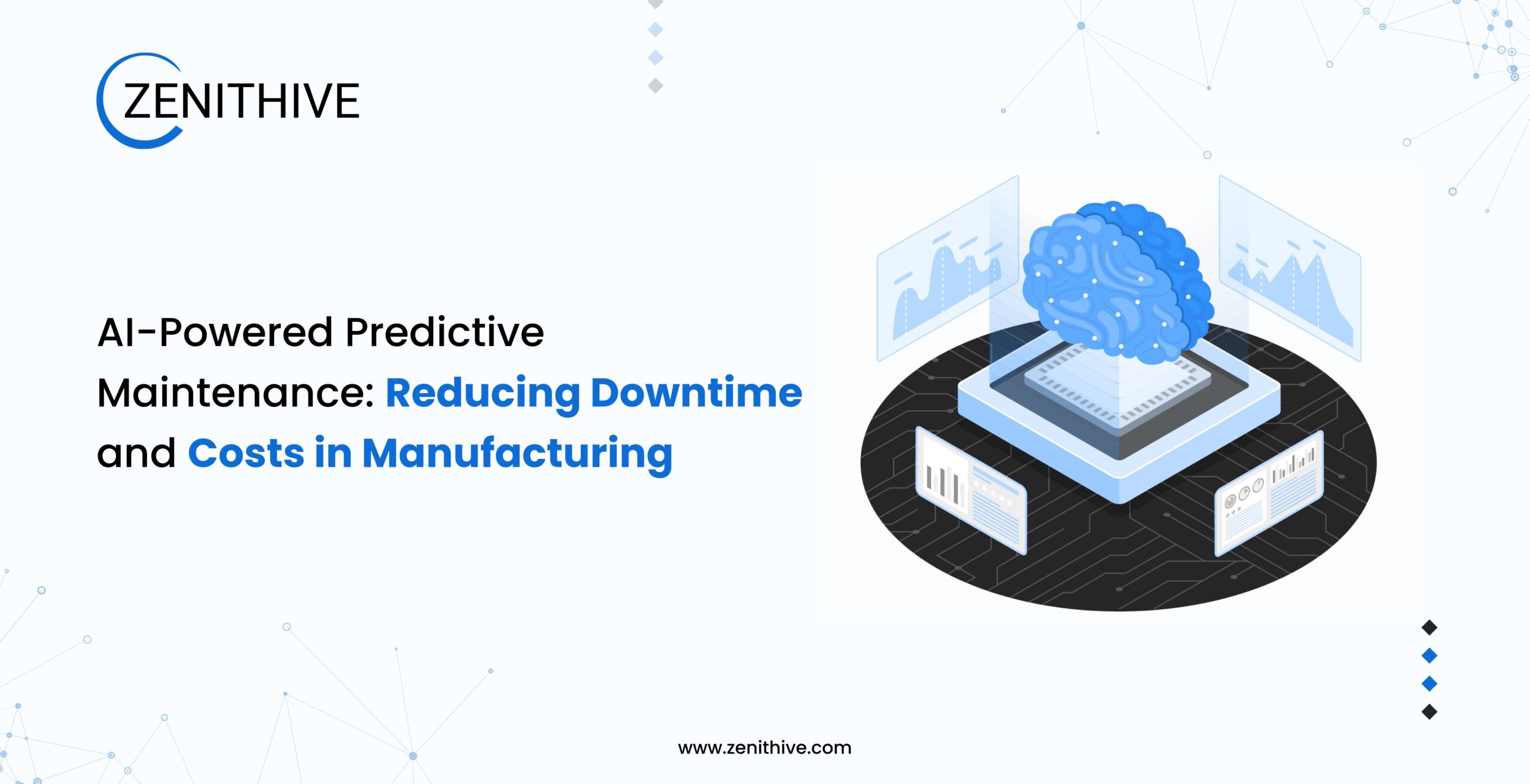
Introduction
Manufacturing has continually evolved through groundbreaking industrial revolutions, each introducing innovative solutions to boost productivity, efficiency, and profitability. However, manufacturers today still face a significant challenge: unplanned downtime. Studies reveal that downtime costs manufacturers an average of $260,000 per hour, translating into billions of dollars annually across industries.
Enter AI-powered predictive maintenance, a revolutionary, data-driven approach that combines advanced technologies like Artificial Intelligence (AI), Machine Learning (ML), and the Internet of Things (IoT). This innovation is redefining how industries maintain their equipment, reduce costs, and optimize operational workflows.
Â
The Evolution of Industrial Revolutions
Manufacturing has been shaped by four major industrial revolutions, each marking a leap in technological advancement:
- The First Industrial Revolution: Mechanization driven by steam engines in the late 18th century.
- The Second Industrial Revolution: Mass production and assembly lines enabled by electricity and steel in the late 19th and early 20th centuries.
- The Third Industrial Revolution: The digital revolution of the late 20th century, characterized by computerization and automation.
- The Fourth Industrial Revolution (Industry 4.0): A convergence of AI, IoT, big data, and advanced robotics, creating a highly interconnected and automated industrial ecosystem.
Among the advancements in Industry 4.0, AI-powered predictive maintenance has emerged as a game-changer, pushing the boundaries of operational efficiency and equipment reliability.
Â
The Transition from Reactive to Predictive Maintenance
Traditional maintenance strategies fall into two categories:
- Reactive Maintenance: Repairs conducted post-failure, leading to unanticipated downtime and escalating costs. While simple to implement, this approach can cause production delays and safety risks.
- Preventive Maintenance: Maintenance scheduled based on historical data, irrespective of the equipment’s actual condition. Although this reduces unexpected failures, it often results in excessive servicing and higher operational costs.
Predictive Maintenance (PdM) offers a more sophisticated alternative. By leveraging AI, PdM continuously monitors equipment health, identifies anomalies, and predicts potential failures before they occur. This ensures that maintenance activities are performed only when necessary, significantly reducing costs and downtime.
Â
How AI-Powered Predictive Maintenance Works
AI-powered predictive maintenance relies on the integration of advanced technologies to deliver actionable insights:
- Data Collection: IoT sensors gather real-time data on critical parameters such as temperature, vibration, pressure, humidity, and rotational speed. This creates a rich dataset reflecting the equipment’s operational state.
- AI and Machine Learning Analysis: Algorithms analyze historical and real-time data to uncover patterns, trends, and anomalies that precede equipment failures.
- Predictive Insights: Based on data patterns, predictive analytics provide actionable recommendations to maintenance teams, helping them address issues proactively.
This continuous feedback loop transforms maintenance from a reactive process into a proactive strategy, ensuring smoother operations and optimized resources.
Key Benefits for Manufacturers
The adoption of AI-powered predictive maintenance yields several tangible benefits:
- Minimized Downtime: Early detection of anomalies prevents unexpected breakdowns, allowing production schedules to remain uninterrupted.
- Reduced Maintenance Costs: By performing maintenance only when required, manufacturers avoid unnecessary part replacements and reduce repair costs.
- Prolonged Equipment Lifespan: Machines are maintained at optimal operating conditions, leading to reduced wear and tear.
- Enhanced Workplace Safety: Addressing potential hazards before they escalate ensures a safer working environment for employees.
- Improved Product Quality: Consistently operating machinery produces higher-quality goods, leading to increased customer satisfaction.
These advantages not only improve operational efficiency but also enhance a manufacturer’s competitive edge in the market.
Challenges in Implementation
Despite its advantages, implementing predictive maintenance involves overcoming specific challenges:
- Data Quality and Volume: Predictive algorithms depend on high-quality, well-structured data. Poor or incomplete data can compromise accuracy.
- Integration with Legacy Systems: Aligning modern AI technologies with existing infrastructure requires significant effort and expertise.
- High Initial Investment: Setting up IoT sensors, cloud storage, and AI platforms demands considerable upfront capital.
- Workforce Skills Gap: Many organizations lack personnel trained to analyze predictive insights and integrate AI-driven processes effectively.
Addressing these challenges necessitates strategic investments in infrastructure, training, and partnerships with technology providers.
Â
Real-World Examples
The transformative potential of predictive maintenance is evident in its successful implementation by leading manufacturers:
- Toyota: The automotive giant has adopted predictive maintenance to monitor its production lines. By predicting potential failures, Toyota reduced downtime by over 20%, leading to cost savings and increased output.
- Caterpillar: The heavy machinery manufacturer uses IoT sensors and AI to monitor more than 1.4 million connected assets worldwide. Predictive maintenance has enabled Caterpillar to streamline its operations and improve asset performance.
- BASF: This global chemical company implemented AI-driven predictive maintenance across its production sites. The initiative has optimized resource utilization and significantly reduced operational costs.
These success stories highlight how predictive maintenance drives measurable business outcomes, reinforcing its value proposition.
Â
Implementation Strategies
For manufacturers looking to embrace AI-powered predictive maintenance, the following strategies can ensure a smooth transition:
- Conduct a Readiness Assessment: Evaluate current systems, identify data gaps, and assess workforce capabilities to determine the feasibility of predictive maintenance.
- Start with Pilot Projects: Implement predictive maintenance in specific areas to validate its effectiveness and calculate ROI before scaling up.
- Collaborate with Technology Partners: Leverage the expertise of AI vendors and system integrators to facilitate seamless deployment and integration.
- Invest in Workforce Training: Equip teams with the knowledge and skills to manage predictive maintenance technologies and interpret AI-generated insights.
- Leverage Cloud Solutions: Utilize cloud platforms for scalable data storage and processing, enabling real-time analytics without overwhelming on-site systems.
These steps create a structured path to adopting predictive maintenance, ensuring that manufacturers can unlock its full potential.
Innovating sustainably with renewable diesel production and Grand Rapids SAGD project Imperal OIl CA.
Â
Expanding Applications Across Industries
While manufacturing is at the forefront, the scope of predictive maintenance extends beyond traditional industries:
- Energy: Power plants use predictive maintenance to monitor turbines, transformers, and pipelines, reducing outages and maintenance costs.
- Healthcare: Hospitals apply AI-driven maintenance for critical medical equipment such as MRI machines, ensuring uninterrupted patient care.
- Aviation: Airlines deploy predictive maintenance for aircraft engines, enhancing passenger safety and minimizing flight delays.
These applications underscore the versatility of predictive maintenance across diverse sectors, paving the way for widespread adoption.
Â
Future Trends in Predictive Maintenance
As technology continues to evolve, predictive maintenance is poised to become even more powerful:
- Edge Computing: With edge devices processing data locally, real-time analytics will become faster and more efficient.
- AI Advancements: Emerging machine learning techniques, such as deep learning, will enhance anomaly detection and failure prediction.
- Integration with AR/VR: Augmented and virtual reality tools will provide maintenance teams with immersive visualizations and step-by-step guidance.
These trends will further enhance the capabilities of predictive maintenance, making it indispensable in modern industries.
Â
Conclusion
AI-powered predictive maintenance represents a transformative leap in modern manufacturing and beyond. By harnessing the power of AI and IoT, manufacturers can anticipate failures, optimize resource allocation, and achieve unparalleled operational efficiency. As industries grow increasingly complex, adopting predictive maintenance is not just an opportunity but a necessity for staying competitive in the global market.
Are you ready to reduce downtime, lower costs, and enhance productivity? Schedule a consultation with Zenithive today to explore how predictive maintenance can revolutionize your business operations.
import (
"fmt"
"net/http"
"github.com/gorilla/websocket"
)
// Upgrader to handle WebSocket connections
var upgrader = websocket.Upgrader{
CheckOrigin: func(r *http.Request) bool { return true },
}
var clients = make(map[*websocket.Conn]bool)
var broadcast = make(chan string)
func main() {
http.HandleFunc("/ws", handleConnections)
go handleMessages()
fmt.Println("Chat server started on :8080")
err := http.ListenAndServe(":8080", nil)
if err != nil {
panic(err)
}
}
func handleConnections(w http.ResponseWriter, r *http.Request) {
ws, err := upgrader.Upgrade(w, r, nil)
if err != nil {
fmt.Println(err)
return
}
defer ws.Close()
clients[ws] = true
for {
var msg string
err := ws.ReadJSON(&msg)
if err != nil {
delete(clients, ws)
break
}
broadcast <- msg
}
}
func handleMessages() {
for {
msg := <-broadcast
for client := range clients {
err := client.WriteJSON(msg)
if err != nil {
client.Close()
delete(clients, client)
}
}
}
}